Regenerative Thermal Oxidizers (RTOs) destroy Hazardous Air Pollutants (HAPs), Volatile Organic Compounds (VOC's) and odorous emissions. PCC's systems achieve emission destruction through the process of high temperature thermal oxidation, utilizing the 3 T's of Destruction, Time, Temperature and Turbulence, at the proper oxygen level to convert the pollutants into carbon dioxide and water vapor.
PCC's RTOs are designed to repurpose the thermal energy generated during operation, reducing the energy consumption and operating costs.
By thoroughly understanding your process, our systems are engineered and designed to optimize performance, maximizing your investment.
0
+Years of Experience and Discovery in Oxidation Technologies
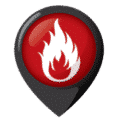
The PCC Difference
Compare the PCC RTO with any others and you'll find these distinct advantages:
The PCC RTO assembly incorporates the inlet and outlet exhaust manifolds into the RTO's overall shell configuration, rather than fabricating the typical network of bulky, exterior space-consuming manifolds. This eliminates external RTO ductwork and insulation, enabling the system to sit flat on a concrete pad without legs.
This streamlined assembly design decreases maintenance costs and creates a compact footprint that is cost-effective to both manufacture and installs.
Our heat recovery chambers are designed to accept all types of media (structured/random packed) including ultra low-pressure drop media specifically designed for use in PCC's RTOs. The combination of high heat recovery with low-pressure drop results in significantly lower gas and electric usage, as well as higher VOC destruction efficiency, making it one of the most environmentally responsible pollution control units available today.
The premise of PCC's RTO design is as simple as 1-2-3:
- Heat is extracted from the hot purified gas and stored in the reheat recovery chamber as it leaves the combustion chamber.
- After a period of time, the inlet/outlet valve switch positions and the contaminated process gas is redirected through the hot heat sink (ceramic media) recovery chamber, where it is preheated to within 5% of the combustion temperature before it enters the combustion chamber. The valve switches on a time base depending on the hydrocarbon loading and heating value (normally every 4 minutes).
- In the combustion chamber, the burner supplements the 5%, bringing its temperature to 1500°F, at which the VOC is converted to harmless CO2 and water vapor.
♦Watch the PCC RTO in action♦
What our customers are saying...
"PCC... The best-kept secret in the industry."
— Rohm & Haas
"PCC works like a well-oiled machine."
— Louisiana Pigments Company
"We would not be where we are today without the engineering knowledge and efforts, quality of construction, professionalism, and cooperation of your first-class organization."
— Montauk Energy Capital
"PCC's commitment to safety and quality allow completion ahead of schedule, under budget, and safely."
—
"PCC's desire to deliver a quality product was apparent throughout all phases of our project, and PCC's overall gas combustion experience resulted in a robust and reliable operating unit."
—
"We are very pleased that it was commissioned five weeks earlier than the contract completion date."
—
"PCC was absolutely on time with delivery of our thermal oxidizer... I was quite impressed. All the units we bought from PCC run flawlessly, even after 10 years. We can't calculate a MTBF, because there have been no failures."
—